Yellow Belt Training Course
MANAGEMENT TRAINING
Training Overview
Why Management
ISO 9001:2015
ISO 14001:2015
ISO 22000:2018
ISO 13485:2016
ISO 45001:2018
View All Programs
QUICK LINKS
Contact Us
Apply for certification
Apply for Job
CONTACT US
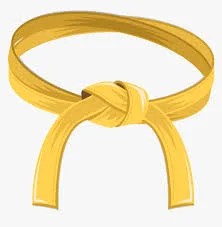
YELLOW BELT TRAINING COURSE:
1. |
COURSE TITLE: |
Yellow Belt Training Course
|
2. |
COURSE PREREQUISITES/ELIGIBILITY: |
Undergraduate/ Graduated |
3. |
NAME OF THE INSTRUCTOR: |
Muhammad Sajjad
|
5. |
START & END DATE/MONTH/YEAR OF THE COURSE |
Depends on batch completion |
6. |
ASSESSMENT MEASURES |
|
COURSE OUTLINE
Module 1: Introduction to Lean Six Sigma
Module 2: Fundamentals of Process Improvement
Module 3: Define Phase
Module 4: Measure Phase
Module 5: Analyze Phase
Module 6: Improve Phase
Module 7: Control Phase
Module 8: Teamwork and Communication
Module 9: Case Studies and Practical Exercises
Module 10: Examination and Certification
|